Calcium hypochlorite is a powder that is often used as a disinfectant, bleach, and water treatment chemical. It is white or light gray in color. It is a significant chemical substance utilized in several processes, such as the construction of industrial chemicals, wastewater treatment facilities, and swimming pools.
Calcium process and sodium process are the two primary ways to make calcium hypochlorite.
According to the Calcium process, the following steps are involved in the manufacture of calcium hypochlorite:
Step 1: calcium hydroxide preparation
The following chemical equation is used to create calcium hydroxide (Ca(OH)2) by reacting calcium oxide (CaO) with water (H2O):
CaO + H2O → Ca(OH)2
A white or gray powder that is just slightly soluble in water is produced as a result of the exothermic process, which produces calcium hydroxide.
Step 2: Calcium hydroxide is chlorinated
According to the following chemical equation, chlorine gas (Cl2) is then used to chlorinate calcium hydroxide:
Ca(OH)2 + 2Cl2 → Ca(ClO)2 + 2H2O
Due to the reaction's strong exothermic potential, it needs to be carefully managed to prevent overheating. To ensure the reactants were evenly mixed and to keep the temperature steady, the reaction mixture was constantly stirred.
Step 3: Drying and packing
The resultant calcium hypochlorite is a hygroscopic powder that is white or light gray in color and may absorb moisture from the atmosphere. To prevent exposure to moisture and sunlight, which can cause the chemical to disintegrate, it is dried to eliminate any remaining water before being stored in an airtight container.
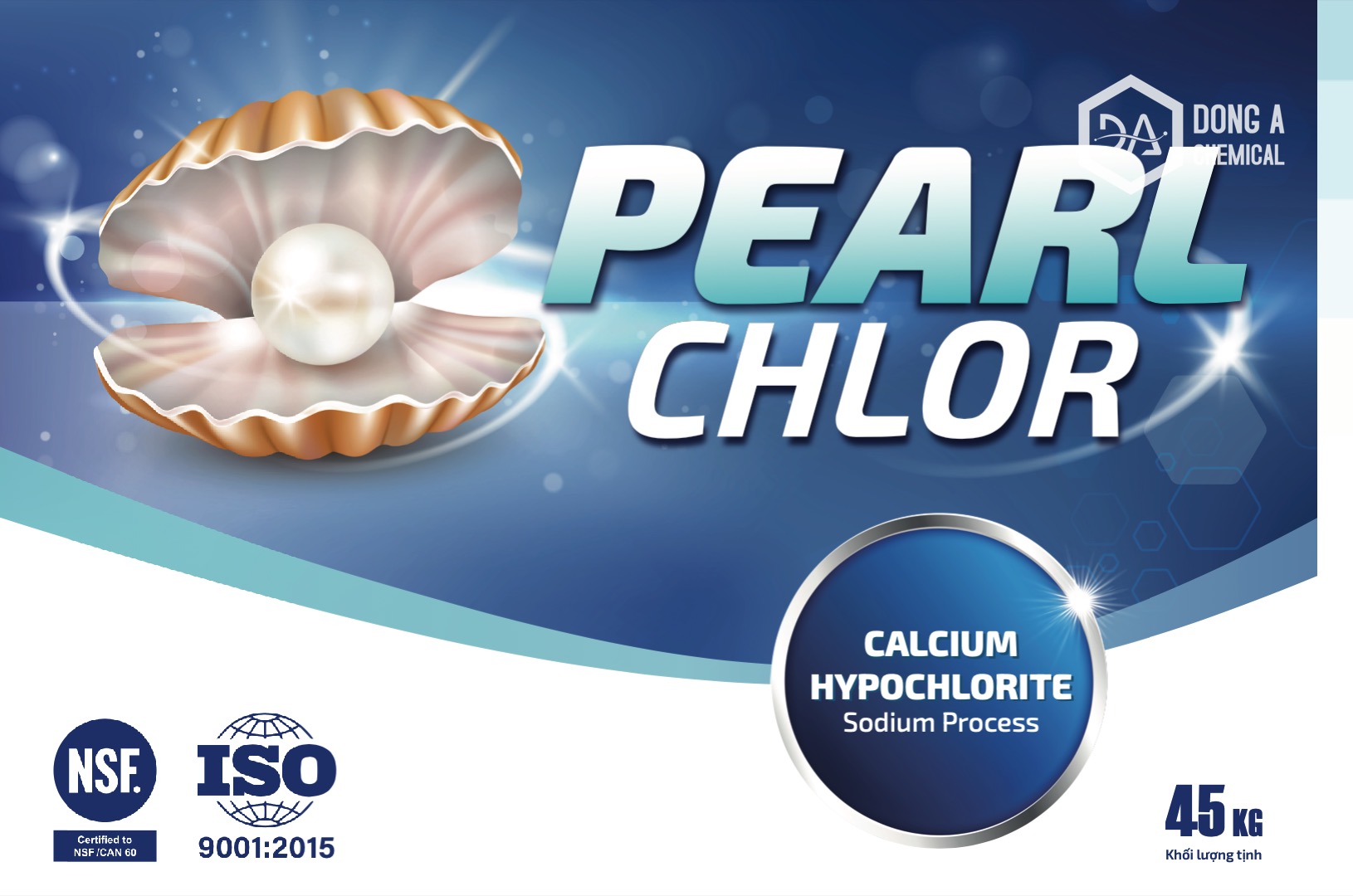
The following steps are included in the sodium process for producing calcium hypochlorite:
Calcium hypochlorite, a significant industrial chemical, is made via the sodium method. In this process, sodium hydroxide (NaOH) and chlorine gas (Cl2) combine to generate sodium hypochlorite (NaClO) as an intermediate, which is then used as a starting material for calcium hydroxide (Ca(OH)2) to react with sodium hypochlorite to form calcium hypochlorite (Ca(ClO)2). Due to its efficiency and simplicity, this method is frequently used to produce calcium hypochlorite.
Reaction mechanism: There are two primary reactions in the sodium process, and they are as follows:
Reaction 1: Production of Sodium hypochlorite
NaOH + Cl2 → NaClO + NaCl
Sodium hypochlorite and sodium chloride are the byproducts of the first process, which involves sodium hydroxide and chlorine gas. Exothermic in nature, this reaction takes place at ambient temperature. Because of its instability and ease of decomposition, the sodium hypochlorite produced in this reaction is employed as an intermediate in the process.
Reaction 2: Production of Calcium hypochlorite
2NaClO + Ca(OH)2 → Ca(ClO)2 + 2NaOH
The second reaction involves the reaction of calcium hydroxide and sodium hypochlorite, which results in the production of sodium hydroxide and calcium hypochlorite as byproducts. With a higher temperature than the previous reaction, this reaction is similarly exothermic. This reaction results in the stable final product calcium hypochlorite, which is useful.
Equipment requirements for the production of Calcium Hypochlorite
To guarantee a safe and effective production process, specialist equipment is needed. In the course of production, the following equipment is frequently used:
- Reaction vessel: A stainless steel or glass-lined vessel is used to hold the reaction mixture and maintain a steady temperature.
- Mixer: To agitate the reaction mixture and make sure the reactants are evenly distributed, a mechanical or magnetic stirrer is utilized.
- Chlorine gas tank: The chlorine gas required for the chlorination process is supplied by a compressed air tank that also contains chlorine gas.
- Equipment for drying: Calcium hypochlorite powder is dried in a fluidized bed dryer or drying oven to eliminate any remaining water.
- Equipment for packaging: A filling and sealing equipment for calcium hypochlorite powder airtight containers.
Safety concerns in the production of calcium hypochlorite
.JPG)
Calcium hypochlorite manufacture is a risky process that calls for stringent safety measures to avoid mishaps and safeguard personnel. Considerations for safety should be given to the following:
- Personal Protective Equipment (PPE): To guard against exposure to chlorine gas and other hazardous chemicals, workers should use the proper PPE, such as gloves, goggles, and respirators.
- Ventilation: To prevent the buildup of hazardous fumes and chlorine gas, the manufacturing space has to be well ventilated.
- Emergency supplies: In case of an emergency, eyewash stations, safety showers, and fire extinguishers should be accessible.
- Training: Employees must get sufficient instruction in the safe handling and use of hazardous chemicals, such as calcium hypochlorite and chlorine gas.
- Maintenance: To guarantee effective operation and to avoid equipment damage or leaks, equipment has to be frequently maintained and inspected.