Calcium hypochlorite is a powder that is often used as a water treatment chemical, disinfectant, and bleach. It is white or light gray in color. It is a significant chemical substance utilized in a variety of settings, including as swimming pools, wastewater treatment facilities, and the manufacture of different industrial chemicals.
Calcium process and sodium process are the two primary ways to make calcium hypochlorite.
According to the Calcium process, the following steps are involved in the manufacture of calcium hypochlorite:
First, make calcium hydroxide.
The following chemical equation is used to create calcium hydroxide (Ca(OH)2) by reacting calcium oxide (CaO) with water (H2O):
H2O + CaO = Ca(OH)2.
A white or gray powder that is just slightly soluble in water is produced as a result of the exothermic process, which produces calcium hydroxide.
Step 2: Calcium hydroxide is chlorinated
According to the following chemical equation, chlorine gas (Cl2) is then used to chlorinate calcium hydroxide:
Ca(OH)2+2Cl2 = Ca(ClO)2+2H2O
Due to the reaction's strong exothermic potential, it needs to be carefully managed to prevent overheating. To ensure the reactants were evenly mixed and to keep the temperature steady, the reaction mixture was constantly stirred.
Step 3: Packing and drying
Calcium hypochlorite, which is the end product, is a hygroscopic powder that can absorb moisture from the atmosphere. It is white or light gray in color. It is then stored in an airtight container after being dried to eliminate any remaining water. This prevents the chemical from being exposed to moisture or sunlight, which might cause it to break down.
The following processes are involved in the synthesis of calcium hypochlorite using the sodium process:
Calcium hypochlorite, a significant industrial chemical, is made via the sodium method. As an intermediary, sodium hydroxide (NaOH) and chlorine gas (Cl2) combine to create sodium hypochlorite (NaClO). Next, calcium hydroxide (Ca(OH)2) reacts with sodium hypochlorite to form sodium hypochlorite. to serve as the final compound Calcium hypochlorite (Ca(ClO)2). This process is widely used in the production of Calcium hypochlorite due to its simplicity and cost effectiveness.
Reaction mechanism: The sodium process has two primary reactions, which are as follows:
Production of sodium hypochlorite results from reaction one.
NaOH + Cl2 → NaClO + NaCl
Sodium hypochlorite and sodium chloride are the byproducts of the first process, which involves sodium hydroxide and chlorine gas. Exothermic in nature, this reaction takes place at ambient temperature. Because of its instability and ease of decomposition, the sodium hypochlorite produced in this reaction is employed as an intermediate in the process.
Production of calcium hypochlorite during reaction two
2NaClO + Ca(OH)2 → Ca(ClO)2 + 2NaOH
In the second reaction, calcium hydroxide and sodium hypochlorite combine to form sodium hydroxide and calcium hypochlorite as byproducts. This reaction takes place at a greater temperature than the previous reaction and is likewise exothermic. The calcium hypochlorite produced in this reaction is stable and can be used as the end product.
Equipment requirements for the production of Calcium Hypochlorite
- To achieve a safe and effective production process, calcium hypochlorite manufacture calls for specific machinery. In the course of manufacturing, the following equipment is frequently used:
- Reaction container: To keep the reaction mixture contained and the temperature consistent, a stainless steel or glass-lined jar is utilized.
- Mixer: To agitate the reaction mixture and guarantee that all of the reactants are evenly mixed, a mechanical or magnetic stirrer is utilized
- Compressed air tank holding chlorine gas is used to supply the chlorine gas required for the chlorination process.
- Drying apparatus: To remove any remaining water from calcium hypochlorite powder, a drying oven or fluidized bed drier is utilized.
- Equipment for packaging: A packing machine that fills and stows powdered calcium hypochlorite in sealed containers.
Manufacturing Calcium Hypochlorite: Safety Considerations
In order to prevent accidents and safeguard personnel, the manufacturing of calcium hypochlorite is a dangerous process that calls for stringent safety measures. It is important to take into mind the following safety factors:
- Workers should use the proper personal protective equipment (PPE), such as gloves, respirators, and goggles, to prevent exposure to chlorine gas and other dangerous chemicals.
- The manufacturing area needs to be well ventilated in order to prevent the buildup of hazardous gasses like chlorine gas.Emergency supplies: In the event of a crisis, fire extinguishers, eyewash stations, and safety showers should be accessible.
- Training: Workers must get sufficient instruction in the safe handling and use of hazardous chemicals, such as chlorine gas and calcium hypochlorite.
- Maintenance: To guarantee optimal operation and to guard against leaks or damage to the equipment, frequent maintenance and inspections are required.
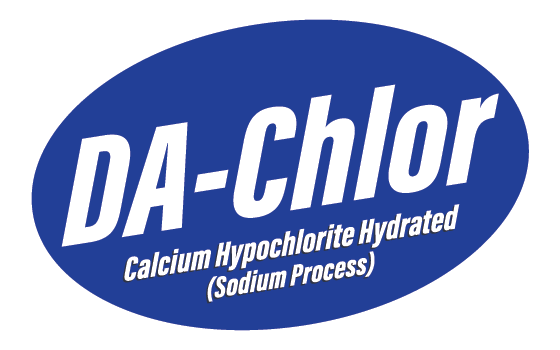
The Dong A chemical firm is now constructing a plant to manufacture and supply Calcium Hypochlorite goods in accordance with the Sodium Process method, which was originally developed in Vietnam. These benefits apply to the Calcium Hypochlorite product from Dong A:
- 65% to 70% for active chlorine.
- Actual chlorine loss Effective yearly loss of chlorine is less than 5% performance index: White homogeneous granules in water that have a faint chlorine odor.
- Stability: Products made using the sodium process have many advantages over those made using the calcium process, including higher thermal stability, better whiteness, less precipitation, etc. The plant bleaching powder fine device introduced is heavy heavy advanced production technology, and the product is first dried before becoming compact, high density, and stable.
- Main Applications: The water treatment sector uses products primarily. It is employed in settings with stringent water quality standards, such as drinking water, swimming pools, and household disinfection, in addition to aquaculture, sanitation, and the control of epidemics.